Sr Technician Mechanical NGLE
Job purpose
Execute Mechanical Maintenance, troubleshooting, and repairs Works for the NGLE, under Shift TL Maintenance (Shift A, B) – Generic scope, acting as Technical Service provider of maintenance and execution of minor projects, modifications in accordance with the technical standards to maintain the assets through:
(1) Execute mechanical maintenance services on planned / un-planned maintenance works utilizing best practice.
(2) Coordination and supervision of assets, products, and maintenance work in the designated area,
(3) Implement plans and coordinate Mechanical maintenance works and
(4) Guide junior Technicians in mechanical maintenance related issues; in order to ensure plant equipment availability, reliability & optimization of cost / resources while facilitating smooth operations of the plant to meet operational targets.
The position will act in accordance with the Group’s Mission, Vision, Values & Strategies, as well as, policies, guidelines, and international standards, supported by an IT Technology platform, HSE standards, Omani’s government & other legal justifications, and best international practices in consonance with national objectives.
Main tasks and responsibilities
Area of scope:
Extraction Unit NGLE
This is the NGL extracted from natural gas from which ethane, propane, n-butane, iso-butane, and pentanes plus are separated by fractionation in a distillation unit.
Static equipment
• Pressure Vessels: containers designed to hold fluids or gases under high pressure (e.g., distillation columns, reactors, and storage tanks).
• Heat Exchangers: devices that facilitate the transfer of heat between fluids at different temperatures and play a vital role in various refinery processes, such as crude oil distillation, catalytic cracking, and hydrotreating.
• Piping Systems: network of pipes that transport fluids between different processing units including pipes, valves, fittings, and supports.
• Storage Tanks: for storing various petroleum products, including crude oil, intermediate products, and finished products, before they are further processed or transported.
• Fired Heaters: for the generation of combustion to heat for processes such as crude oil heating, reforming, and cracking.
Rotating Equipment:
• Pumps: including centrifugal pumps, positive displacement pumps, and reciprocating pumps. Pumps are used for fluid transfer, boosting pressure, and circulation within the refinery.
• Compressors: to increase the pressure of gases, including process gases, fuel gases, and air. They are essential for processes such as hydrogen production, gas sweetening, and catalytic cracking.
• Turbines: to convert fluid energy into mechanical energy and are utilized in various applications, such as driving compressors, generators, and other rotating equipment.
• Fans and Blowers: for air movement, ventilation, and combustion air supply in different refinery units, including cooling towers and furnaces.
Responsibilities:
Static Equipment
• Manages the task distribution within the team, for performing planned / unplanned / shutdowns, turnarounds etc. of Static Equipment including tanks, vessels, furnaces, heat exchangers, valves piping, painting, Insulation, and scaffolding
• Close coordination with Operations teams for routine works and troubleshooting of static equipment.
• Participate along with the team in the Safe and Efficient delivery of the NGLE plant Maintenance Execution Plans for static equipment’s.
• Attend internal meeting (Operation, TSD, Planning & other department involves in planned Static maintenance activities) to discuss and proactively resolve issues.
• Assist Engineers for inputs on technical evaluation for RFQ.
• Provide maintenance support in general or by on-call or shift coverage for Static equipment’s.
• Manage planned material and spare withdrawals from inventory and return of unutilized items.
• Perform proper utilization of processes in SAP (notification and work order updates, breakdown notifications, failure reporting etc.) as per procedures.
• Participate in major equipment trips and failure investigations – Root Cause Analyses (RCA).
• Participate in Job Safety Analysis (JSA).
• Ensure maximum availability of plant Static assets and Scaffolding optimization through optimum use of resources in order to meet plant targets.
• Develop & implement solutions to maintenance process & activities ensuring risk of failures are fully detected, understood and mitigated.
• Ensure that effective execution of planned maintenance activities /services are carried out & completed in accordance to maintenance best practice and within time frame.
Rotary Equipment
• Perform proper utilization of maintenance and upkeep for all the Rotary as well as Static equipment in the area assigned to ensure highest level of Reliability and availability.
• Assist the Engineers on development of Maintenance plan, Maintenance task list.
• Participate in developing the MCP (Maintenance Craft procedures) for all the Rotary equipment’s in the area in consideration to Vendor Manuals, International best maintenance practices, Codes and standard and guidelines issued by TSD.
• Ensure all the special tools and materials and spares availability for the planned and corrective repairs on a daily basis.
• Attend internal meeting (Operation, TSD, Planning & other department involves in planned Mechanical maintenance activities) to discuss and proactively resolve issues and work prioritization.
• Ensure all planned maintenance activities (CM, PM and TA) work orders are communicated with supervisors (Company/ contract) and are executed as per plan.
• Ensure to enter rotating equipment maintenance history & reports are updated in SAP (CMMS)
• Ensure approved planned maintenance sequential of activities & work prioritization and availability of required resources (spare parts, tools, drawings & manpower) are carried out accordingly as per scheduled.
• Attends daily meetings & communicates with Operation, TSD, Planning, HSE and other departments for coordination of mechanical maintenance activities.
• Participate in Indenting the critical issues, repetitive failure of rotating equipment and work to perform the (RCA)
Repair and Replacement:
• Replace faulty mechanical components, such as pumps, motors, valves, bearings, belts, and gears, following safety protocols and manufacturer guidelines.
• Repair or replace mechanical parts, ensuring compliance with equipment specifications and industry standards.
• Maintain an inventory of mechanical spare parts and equipment and coordinate with procurement for timely replenishment.
• Monitor and track equipment performance, identify trends, and propose improvements to enhance reliability and efficiency
Safety and Compliance:
• Adhere to safety protocols, lockout/tagout procedures, and other relevant safety regulations while performing mechanical maintenance tasks.
• Follow maintenance procedures, equipment manuals, and industry best practices to ensure compliance and prevent accidents.
• Participate in safety meetings, training sessions, and incident investigations to promote a safe working environment.
• Report any safety concerns, near misses, or incidents related to mechanical systems and equipment.
Documentation and Reporting • Maintain accurate records of mechanical maintenance activities, including work orders, inspection reports, and equipment history.
• Update equipment manuals, procedures, and documentation as required to reflect changes or modifications.
• Generate reports on equipment performance, maintenance activities, and recommendations for improvements.
• Provide input for the development of maintenance procedures, guidelines, and standard operating procedures (SOPs).
Collaboration and Communication
• Coordinate with the operations team to ensure minimal disruption to operations during maintenance activities.
• Collaborate with other maintenance technicians, engineers, and contractors to optimize maintenance schedules and resource allocation.
• Communicate effectively with Engineers, team members, and stakeholders to report progress, issues, and any potential impact on operations.
• Actively participate in team meetings, training sessions, and knowledge-sharing activities.
Key interactions
Internal: Field Operators, Shift Team Leader, Panel Operators, Maintenance Coordinator, Process Trainer, Technical Services Department, Sr. / Engineer Operations.
External: Maintenance contractor Manpower and OEM for technical inquiry
Notable Working Conditions. Field Operations and office environment, Moderate to intensive computer screen use.
Education requirements
• Minimum Qualifications for this position are Diploma in Mechanical Engineering or similar
• Relevant certification or license in Mechanical maintenance is desirable but not required.
Language requirements Excellent knowledge of written, read, and spoken English (required) | Arabic – Native (desirable)
Background and experience
• 2+ years of relevant experience
• Experience and knowledge in installation, trouble shooting, and start-up on process plant.
• Sound judgment in technical matters with good skills in engineering field materials specifications and international standards.
• Good experience in handling of Maintenance Contracts and shutdown related jobs.
Knowledge of :
– Computerized Maintenance Management Systems (CMMS)
– Expertise in SAP- PM
• Broad understanding of relevant processes, plant and equipment regarding Static equipment.
• Knowledge in operating and maintaining the reliability of all Rotating equipment.
• Experience in condition monitoring systems on Static and Rotating equipment.
• Good knowledge in Quality Assurance, Quality Control and HSE plans.
• Familiar with techniques for ensuring data integrity with various integration of information/ reports
• Knowledgeable in HSE plans related to maintenance activities.
• Understanding of Process (P&IDs / PFDs) & Engineering drawings and OEM manuals. Soft:
• Verbal and writing reporting skills-effective Communication
• Able to build relationships within department staff and contractors with a focus on collaboration.
• Ability to manage multiple priorities in a diversified and critical environment.
Technical:
• Through use of facts
• Troubleshooting and result oriented
• Root Cause Analysis (RCA)
• Reading and interpreting engineering drawings
• Developing and Modifying Technical Procedures
• Ability to align the requirements of operations and maintenance
• Ability to supervise the job with quality work & timely completion.
Job Req ID: 55901
Date: Jul 14, 2024
Location:
Fahud, OM
Entity: OQ Refineries and Petrol
Business Unit: RPI Operations
Division: LPIC
Country/Region: OM
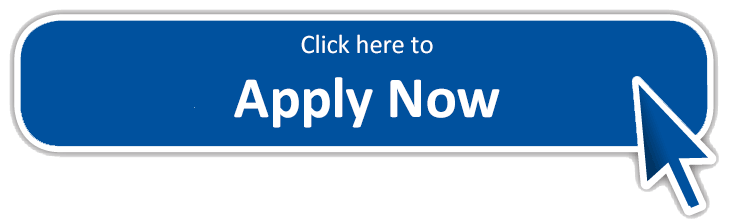
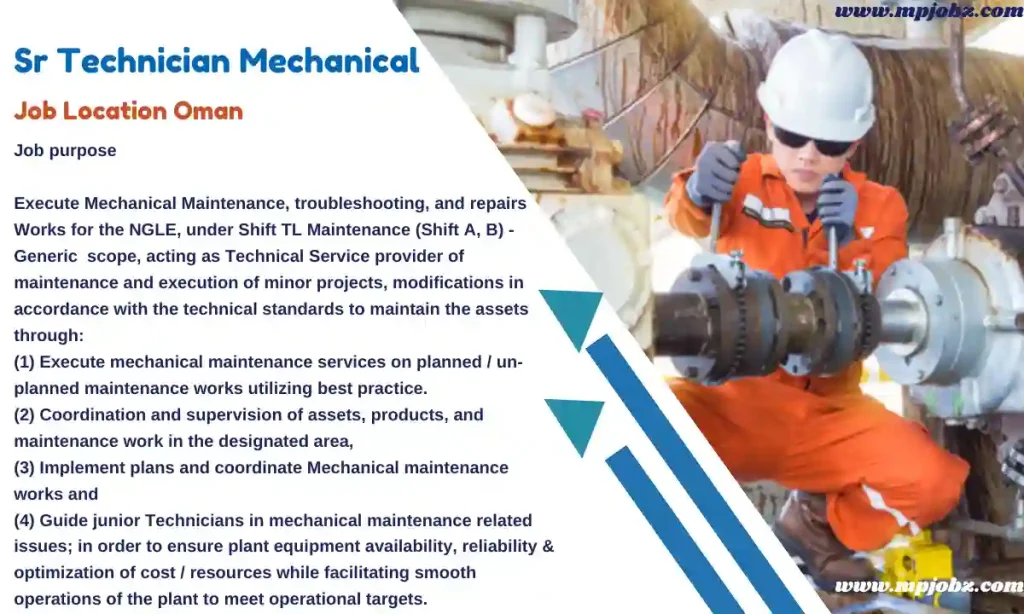